Solving the problem of process efficiency has two positive effects.
First of all, introducing coil-fed processing into the process – as we've seen – produces raw material savings that can even be in excess of twenty percent for the same quantity of product and that means positive margins and cash flow that is immediately available to the company.
This may vary depending on sector and use: in any event, it's material that the entrepreneur and the company no longer have to purchase and the waste also doesn't need to be managed or disposed of.
The whole process is much more profitable and the positive result can be seen immediately on the income statement.
Furthermore, by purchasing less raw material, the company automatically makes the process more sustainable, because that raw material no longer needs to be produced downstream!
Energy efficiency is another important element in the cost of each production cycle.
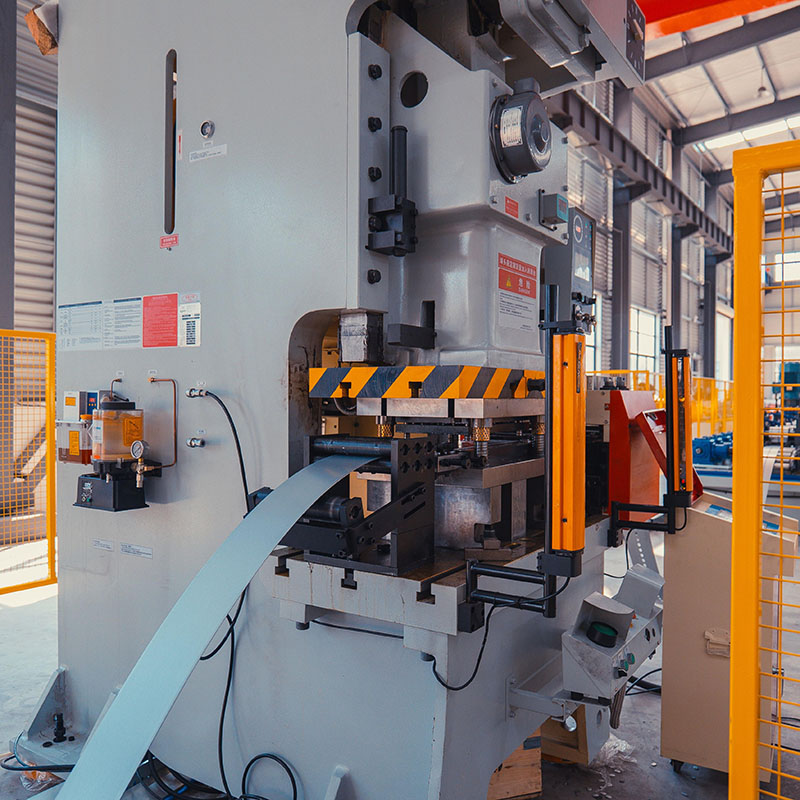
In a modern production system, the consumption of a roll forming machine is relatively low. Thanks to the Combi system, lines can be equipped with several small motors driven by inverters (instead of one, large special motor).
The energy used is exactly that required by the forming process, plus any friction in the transmission parts.
In the past, a big issue with fast fly cutting machines was the energy dissipated via the braking resistors. Indeed, the cutting unit accelerated and decelerated continuously, with a great expenditure of energy.
Nowadays, thanks to modern circuits, we can accumulate energy during braking and use it in the roll forming process and in the subsequent acceleration cycle, recovering much of it and making it available to the system and to other processes.
Furthermore, almost all electrical movements are managed by digital inverters: compared to a traditional solution, energy recovery can amount up to 47 percent!
Another problem regarding the energy balance of a machine is the presence of hydraulic actuators.
Hydraulics still perform a very important function in machines: there are currently no servo-electric actuators capable of generating so much force in so little space.
Regarding coil-fed punching machines, in the early years we only used hydraulic cylinders as actuators for the punches.
The machines and customer needs continued to grow and so did the size of the hydraulic power units used on machines.
Hydraulic power units bring oil under pressure and distribute it to the entire line, with consequent drops in pressure levels.
The oil then heats up and a lot of energy is wasted.
In 2012, we introduced the first servo-electric coil-fed punching machine onto the market.
On this machine, we replaced the many hydraulic actuators with a single electric head, managed by a brushless motor, which developed up to 30 tons.
This solution meant that the energy required by the motor was always only that required for cutting the material.
These servo-electric machines also consume 73% less than similar hydraulic versions and also provide other benefits.
Indeed, hydraulic oil needs to be changed approximately every 2,000 hours; in the event of leaks or broken tubes, it takes a long time to clean up and refill, not to mention the maintenance costs and checks related to a hydraulic system.
However, the servo-electric solution only requires the refilling of the small lubricant tank and the machine can also be fully checked, even remotely, by an operator and a service technician.
In addition, servo-electric solutions offer about 22% faster turnaround times compared to hydraulic technology.Hydraulic technology cannot yet be completely eliminated from processes, but our research and development is certainly directed towards the increasingly widespread use of servo-electric solutions due to the numerous benefits they provide.
Post time: Mar-23-2022